Press decorative panels with white glue (PVA glue)
In order to obtain a compact design board with a decorative panel with material thicknesses of 1-4 mm, the design sheet can be pressed. Due to the rigid adhesive connection between the decorative panel and the wooden beams, the finished board does not extend anymore and can therefore either be processed seamlessly on walls, or furniture fronts can be made.
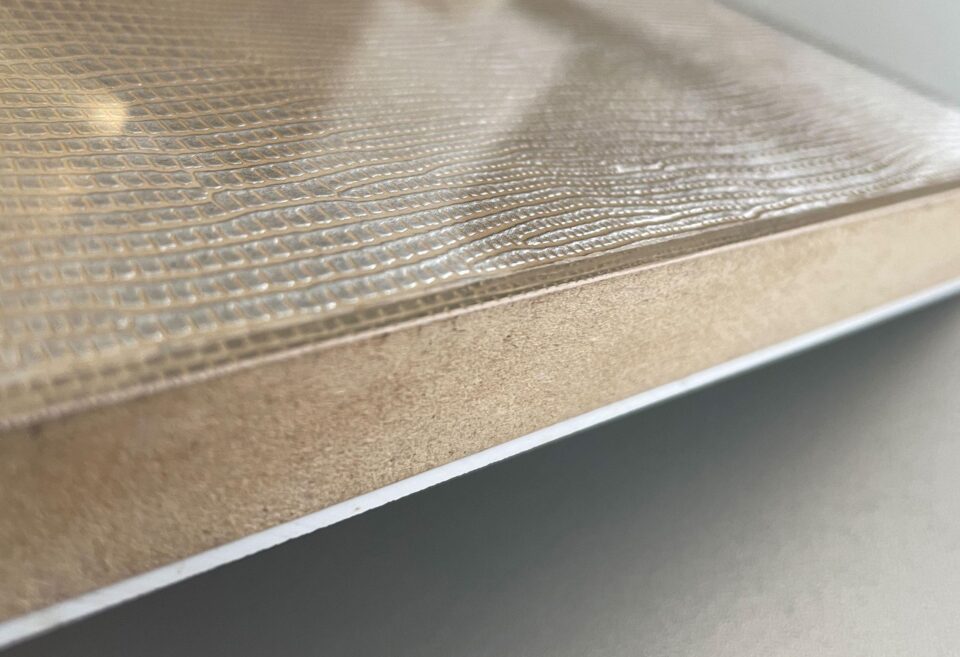
Cross-section pressed plate with counter tension
Pre-treatment of the non-adhesive design plate
In order to get suitable design sheets for PVA bonding (pressing with white glue), depending on the material, they either have to be pretreated on the back with an additional production step at SIBU DESIGN or sanded manually, i.e. roughened.
Since the production process is not done automatically , the PVA pretreatment must be advised with the order. The pretreatment carried out by SIBU DESIGN is an industrial treatment with electrons to increase the surface tension. Since the effect of the treatment decreases again over time, the design panel pretreated by SIBU must be pressed within 2 months after the delivery date.
Alternatively, you can treat the decorative sheet yourself to achieve an optimal surface tension. A manual follow-up treatment is also necessary if the decorative panels pretreated by SIBU Design have not been pressed for more than 2 months. To check whether the surface tension is still sufficient for pressing, you can use a test ink to measure the surface tension. The surface tension should be at least 46mN/m.
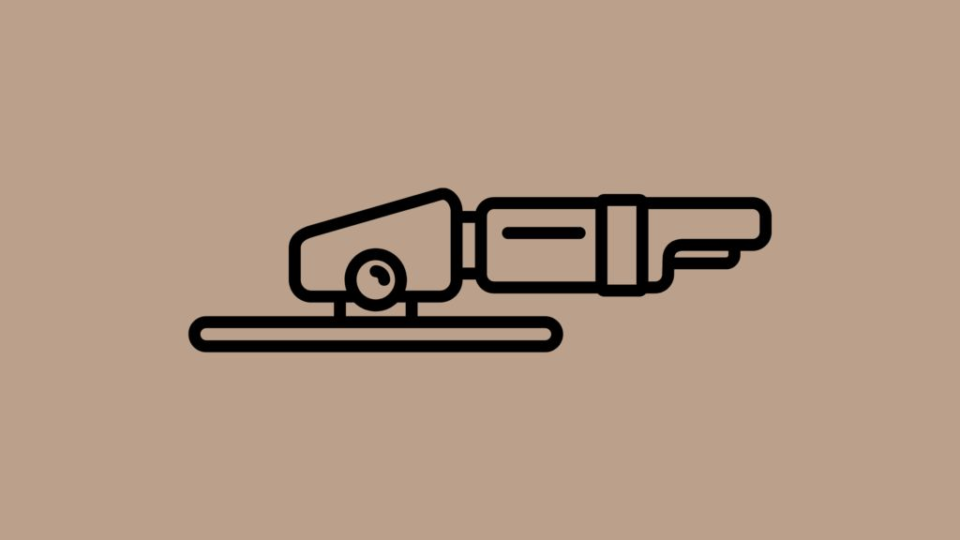
Do all decorative panels have to be pre-treated?
Can all design panels be pressed?
Due to different material characteristics, there are a few products that are not suitable for PVA bonding. Please refer to the technical spreadsheet of the product to see if pressing is possible.
Principally, the following product groups/products are not suitable for pressing
(MS) MULTISTYLE – Products: Mirror mosaic panels are only available in self-adhesive – therefore unsuitable for PVA bonding.
(PL / PL3D) PUNCH-LINE / 3D – Products: Perforated sheets with effect foil and therefore not useful for pressing
(TL) TRANSLUCENT-LINE: Semi-transparent decorative sheets with millings are translucent and can therefore be backlit, PVA pressing doesn’t makes any sense (technically possible – but the effect of backlighting gets lost)
(LL) LEATHER-LINE: Some products of this product group can’t be pressed, e.g. LL ROMBO
(BA) BATH ART MATT: If PVA bonding is being considered, we recommend to use the corresponding STRUCTURE-LINE designs for pressing
SG Hollywood: is not suitable for grouting due to its transparency.
Antigrav & NATURE-LINE: Products with the addition “Antigrav” or “Nature” are not suitable for grouting.
Material requirements & preparation
For pressing the following is required:
- Decorative panel in non-adhesive (NA) version, with a surface tension of at least 46mN/m (achieved by SIBU DESIGN PVA treatment or by manual sanding)
- Absorbent wooden material (e.g. MDF or chipboard) – only use flat and calibrated wooden based boards.
- Sheet press
- White glue
- Balancing sheet- material and material thickness need to be adjusted to the decorative panel
Preparation:
The two press sheets must be cleaned carefully before starting! Even minimal dirt has a negative effect on the decorative surface.
Sweep or blow off the wooden panel material cleanly. The back of the design sheet must also be clean and dust-free before pressing, so it is recommended to wear gloves during the process to prevent to damage the back. Before pressing, check the surface for any damage!
Appropriate return
So that the finished pressed panel remains flat and distortion free, it is necessary to choose a suitable balancing sheet that matches the decorative panel acoording to it’s material characteristics and thickness.
On request, we can offer technically coordinated balancing sheets. Which balancing sheet you need to order can be seen in the technical spreadsheet of each product.
Apply white glue
- Lay the acclimatized SIBU decorative panel, balancing sheet and wooden based panel next to each other on a straight, clean and sufficiently large working table.
- The wooden based panel is cut approx. 10 mm bigger than the design sheet/balancing sheet.
- First of all put the PVA glue on the back of the design and balancing sheet using a glue roller – as evenly and over the entire surface as much as possible!
- Then both SIBU DESIGN sheets are put in the middle of the wooden support panel as soon as possible. No direct application of glue on the wooden carrier board – this can have a negative effect on the flatness.
- Afterwards the composite goes into the plate press.
SIBUGLAS with synthetic fibre backing: The consumption of PVA white glue is slightly higher due to the absorbent synthetic fibre backing. The glue consumption is approx. 200 – 300 g/m2. The synthetic fibre should have a wet adhesive sheen shortly before gluing.
Pressing in the plate press
If the design sheet does not have a wrinkle-free protection foil due to transport or storage conditions, it must be removed before the pressing process.
STRUCTURE-, FABRIC-, LEATHER & WOOD-LINE
During the pressing process a medium-hard foam rubber mat with a thickness of approx. 5 mm must be put between the pressing sheet and the decorative side of the sheet. It achieves an even pressure distribution and at the same time it avoids unwanted pressure marks caused by dirt particles between the press plate and the design panel.
Do not press with too much pressure, use your own experience and know-how!
Guideline: The press force should be around 2 kg/cm² (0.2 N/mm²), the temperature around 45°C and the pressing time approx. 15 minutes.
If the guidelines for the pressing time of the used white glue differ, the basic rule is: add 1 minute of pressing time per mm of material thickness or additional enclosure such as foam rubber.
DECO-LINE
Flat design panels are better being pressed without a foam rubber. The foam rubber could make the surface seem too uneven. In order to esaier get a smooth surface, ask us for decorative sheets in 2mm thickness.
ATTENTION: When pressing mirror or high-gloss products, an absolutely undamaged, clean pressing plate is required.
Do not press with too much pressure, use your own experience and know-how!
Guideline: The press force should be around 2 kg/cm² (0.2 N/mm²), the temperature around 45°C and the pressing time approx. 15 minutes.
If the guidelines for the pressing time of the used white glue differ, the basic rule is: add 1 minute of pressing time per mm of material thickness
SIBUGLAS | OPACO-LINE
Do not press with too much pressure, use your own experience and know-how!
Guideline: The press force should be around 2 kg/cm² (0.2 N/mm²), the temperature around 30°C and the pressing time approx. 30 minutes.
If the guidelines for the pressing time of the used white glue differ, the basic rule is: add 1 minute of pressing time per mm of material thickness
- As soon as the sheets are removed from the press, they must be stored flat in stack pressure.
- A really even base is important for the flatness of the bonded panel!
- Cover the stack with 19 mm chipboard so that the top board can also be laid out flat.
- Let the panels cool down in the stack after the pressing process – preferably overnight (for at least 12 hours).
A second option for small quantities is to press the panels in the machine overnight at around 20 °C. This type of processing does not require stack pressure afterwards.
Processing of the pressed design panel
Glued and pressed panels can be processed simply with most of the standard woodworking machines and woodworking tools.
During the process, the PE protective film must remain on the surface. The use of suitable and well-cutting tools prevents damage. Ideal machine parameters, tool design and cutting speeds have to be observed individually with a sample production before the manufacture.
The finished pressed design panels can be easily cut to size with a saw and then be provided with commerical edges made of plastic, aluminium or wood.